LMD技術(shù)作為快速成型制造技術(shù)的一種,是通過快速成型(RapidPrototyping,RP)技術(shù)和激光熔覆技術(shù)有機結(jié)合,以金屬粉末為加工原料,采用高能密度激光束將噴灑在金屬基板上的粉末逐層熔覆堆積,從而形成金屬零件的制造技術(shù)。整個LMD系統(tǒng)包括激光器、激光制冷機組、激光光路系統(tǒng)、激光加工機床、激光熔化沉積腔、送粉系統(tǒng)及工藝監(jiān)控系統(tǒng)等。
LMD技術(shù)國外發(fā)展現(xiàn)狀
增材制造技術(shù)發(fā)展經(jīng)歷了3個階段,1892~1988年的技術(shù)孕育期、1988年開始的快速原型技術(shù)及20世紀90年代初期以來的直接增材制造。1979年,UTRC提出激光立體成形技術(shù)概念并制作出航空發(fā)動機渦輪盤模擬件;1994年起,Rolls-Royce探索航空發(fā)動機零件激光成形,另外英國利物浦大學和美國密西根大學、加拿大國家研究委員會集成制造技術(shù)研究所、瑞士洛桑理工學院、美國Sandia國家實驗室、美國Los-Alamos國家實驗室、美國Aeromet公司、美國賓州大學、英國伯明翰大學等都相繼開展研究。由于LMD同軸送粉效率高,材料致密性好,因此,越來越多的用于大型零件的增材制造及零件修復工作。
國外有關(guān)大型零件增材制造技術(shù)的研究主要集中在美國。1995~2005年間,在美國國防部先進研究計劃署及海軍研究辦公室等部門的巨額資助下,美國約翰哈普金斯大學、賓夕法尼亞州立大學及MTS公司等對飛機鈦合金結(jié)構(gòu)件激光快速成形技術(shù)進行了大量研究并取得重大進展,在此基礎(chǔ)上,1998年由MTS公司獨資成立了專門從事飛機鈦合金結(jié)構(gòu)件激光快速成形制造技術(shù)研發(fā)和工程化應用的AeroMet公司,與波音、洛克希德·馬丁及諾斯羅普·格魯曼等美國三大軍用飛機制造商合作,在美國空軍“鍛造計劃”(AirForce’sForgingInitiative)、陸軍制造技術(shù)計劃(Army’sMantechProgram)、國防部“軍民兩用科技計劃”(DualUseScienceandTechnologyProgram)等資助下,致力于飛機鈦合金結(jié)構(gòu)件激光快速成形技術(shù)研究及其在飛機上的應用關(guān)鍵技術(shù)研究。2000年9月在波音和洛克希德·馬丁公司完成了對激光直接成形鈦合金全尺寸飛機機翼次承力結(jié)構(gòu)件研究,構(gòu)件靜強度及疲勞強度達到飛機設(shè)計要求;2001年為波音公司F/A-18E/F艦載聯(lián)合殲擊/攻擊機驗證機小批量試制了發(fā)動機艙推力拉梁、機翼轉(zhuǎn)動折疊接頭、翼梁、帶筋壁板等飛機鈦合金次承力結(jié)構(gòu)件,其中F/A-l8E/F翼根吊環(huán)滿足疲勞壽命譜4倍要求,隨后靜力加載到225%也不破壞;2002年實現(xiàn)激光快速成形鈦合金次承力結(jié)構(gòu)件在F/A-18驗證機上的裝機應用。此外,美國還將應用于F-22接頭的制造,試驗結(jié)果表明其疲勞壽命高出壽命譜的兩倍。
在LMD技術(shù)取得一定突破的時候,國外還將該技術(shù)廣泛用于損傷零件的修復,包括飛機零部件腐蝕零件、航空發(fā)動機磨損等零件的修復。美國AeroMet公司采用激光成形技術(shù)完成了F15戰(zhàn)斗機中機翼梁的檢修;美國Optomec Design公司,采用激光成形技術(shù)進行了T700美國海軍飛機發(fā)動機零件的磨損修復;瑞士洛桑理工學院采用激光成形技術(shù)修復單晶渦輪葉片。
LMD技術(shù)國內(nèi)發(fā)展現(xiàn)狀
我國在金屬材料增材制造領(lǐng)域研究起步較早,技術(shù)研究及應用方面具有良好的基礎(chǔ),特別是在國家自然科學基金“重點項目”、國家“973”項目、國家“863”等重要研究計劃重點支持下,增材制造技術(shù)得以快速發(fā)展。整個研究工作主要集中于北京航空航天大學、西北工業(yè)大學、北京有色金屬研究總院、華中科技大學、清華大學等單位。其中在LMD技術(shù)領(lǐng)域上主要以北京航空航天大學、西北工業(yè)大學等少數(shù)幾家單位。
在“十五”期間,北京航空航天大學突破了飛機鈦合金次承力結(jié)構(gòu)件激光快速成形工藝及應用關(guān)鍵技術(shù),構(gòu)件疲勞、斷裂韌性等主要力學性能達到鈦合金模鍛件水平,2005年成功實現(xiàn)激光快速成形TA15鈦合金飛機角盒、TC4鈦合金飛機座椅支座及腹鰭接頭等4種飛機鈦合金次承力結(jié)構(gòu)件(如圖1所示)在3種飛機上的裝機應用。
“十一五”期間,北京航空航天大學在飛機鈦合金大型整體主承力結(jié)構(gòu)件激光快速成形工藝研究、工程化成套裝備研發(fā)與裝機應用關(guān)鍵技術(shù)攻關(guān)等方面取得了突破性進展,提出了大型金屬構(gòu)件激光直接成形過程“內(nèi)應力離散控制”新方法,初步突破大型金屬構(gòu)件激光快速成形過程零件翹曲變形與開裂“瓶頸難題”;突破激光快速成形鈦合金大型結(jié)構(gòu)件內(nèi)部缺陷和內(nèi)部質(zhì)量控制及其無損檢驗關(guān)鍵技術(shù),飛機構(gòu)件綜合力學性能達到或超過鈦合金模鍛件,例如,激光快速成形TA15鈦合金缺口疲勞極限超過鈦合金模鍛件32~53%、高溫持久壽命較模鍛件提高4倍(500℃/480MPa持久壽命由鍛件不足50h提高到激光成形件230h以上),特別是經(jīng)后續(xù)特種熱處理新工藝獲得“特種雙態(tài)組織”(圖2所示)后,其綜合力學性能進一步顯著提高,疲勞力紋擴展速率降低一個數(shù)量級以上(圖3)。
此外,激光快速成形出TA15、TC4、TC21、TC18、TC2等鈦合金先進飛機大型整體主承力關(guān)鍵結(jié)構(gòu)件、A-100等超高強度鋼起落架等飛機關(guān)鍵構(gòu)件、TC11、TC17、Ti60等鈦合金整體葉盤等航空發(fā)動機關(guān)鍵部件并在飛機研制和生產(chǎn)中得到成功應用。
西北工業(yè)大學自1995年開始,在國內(nèi)首先創(chuàng)造性地提出以獲得極高力學性能為目標的金屬增材成形技術(shù)構(gòu)思,賦予“激光立體成形”之名,依托凝固技術(shù)國家重點實驗室開展了系統(tǒng)的研究工作,建立起了包含材料、工藝和裝備技術(shù)的完整的技術(shù)體系。經(jīng)過近20余年的研究,針對大型鈦合金構(gòu)件的激光立體成形,解決了大型構(gòu)件變形控制、幾何尺寸控制、冶金質(zhì)量控制、系統(tǒng)裝備等方面的一系列難題,并試制成功C919大飛機翼肋TC4上、下緣條構(gòu)件,該類零件尺寸達450mm×350mm×3000mm(圖4),成形后長時間放置后的最大變形量小于1mm,靜載力學性能的穩(wěn)定性優(yōu)于1%,疲勞性能也優(yōu)于同類鍛件的性能。此外,在LMD技術(shù)零件修復方面也取得了重大進展。TC4激光修復試樣在低應變區(qū)的疲勞壽命高于鍛件,在高應變區(qū)低于鍛件,經(jīng)過噴丸處理后及匹配修復后,高應變區(qū)疲勞壽命已非常接近鍛件;圖5所示為航空發(fā)動機軸承后機匣激光修復,通過激光修復軸孔徑向缺陷,成形前安裝邊,恢復零件設(shè)計結(jié)構(gòu)及尺寸,為該發(fā)動機首次裝機試車提供合格零件;此外,還成功的應用于鋁合金導向葉片、不銹鋼機匣、鈦合金壓氣機靜子葉片、鎳基合金高壓一級渦輪葉片等修復。
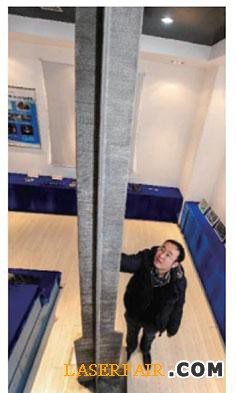
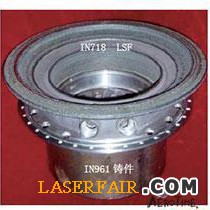