在過去十年間,作為越來越精密的結(jié)構(gòu)和功能組件,玻璃在平板顯示器、汽車和建筑等各領(lǐng)域的應(yīng)用廣泛。這推動(dòng)著玻璃制造商改善玻璃自身的特性、研發(fā)更先進(jìn)的玻璃涂料,以及改進(jìn)玻璃切割工藝,具體而言包括提高切割精度、加快切割速度、減少對環(huán)境的影響,以及降低切割成本。本文概要介紹玻璃激光切割技術(shù),并探究在某些應(yīng)用環(huán)境中,激光切割相較于傳統(tǒng)機(jī)械加工法的優(yōu)勢。
傳統(tǒng)方法
人們通過各種形式的傳統(tǒng)技術(shù)切割玻璃幾乎已有幾個(gè)世紀(jì),也就是先用鋒利的堅(jiān)硬工具(通常為金剛石或碳化物砂輪)刻劃玻璃表面,然后施加機(jī)械掰斷力,讓玻璃沿劃痕完全分離。在自動(dòng)式系統(tǒng)中,玻璃分離往往是由壓到玻璃上的“閘刀桿”實(shí)現(xiàn)。
遺憾的是,這種方法有許多缺陷,尤其在如今平板顯示器 (FPD) 中越來越多采用超薄基板的環(huán)境中,這些缺陷更加明顯。主要缺陷在于刻劃工具施加的機(jī)械力會(huì)讓材料產(chǎn)生細(xì)微裂紋、后續(xù)掰斷步驟會(huì)造成小缺口和碎屑,而且切割邊緣也不一定與玻璃表面垂直。另外,機(jī)械切割會(huì)在成品邊緣留下相當(dāng)大的機(jī)械應(yīng)力。(實(shí)際上,當(dāng)基板厚度小于 1 毫米時(shí),由于玻璃特別容易斷裂,因此很難使用機(jī)械切割法。)為了防止玻璃在經(jīng)受首道切割工序之后出現(xiàn)破裂或斷裂,可能必須對切割表面進(jìn)行打磨或拋光。另外,加工后可能還必須安排清潔環(huán)節(jié)來清除可能對后續(xù)流程(例如電路形成)造成干擾的碎屑(當(dāng)玻璃用作微電子制造中的基板時(shí))。
對制造商而言,在加工后安排各種邊緣打磨和清潔環(huán)節(jié)無疑會(huì)額外增加制造工時(shí)和成本。這些環(huán)節(jié)也可能會(huì)對環(huán)境造成負(fù)面影響,包括產(chǎn)生不易處理的碎屑,或?yàn)榱诉M(jìn)行清潔需要耗用大量水資源。另外,如今對曲線邊緣(尤其是用于便攜式設(shè)備的 FPD)的需求量越來越大,而玻璃機(jī)械切割法對切割曲線邊緣的支持度卻不高。
鑒于當(dāng)今的玻璃使用趨勢,上述這些局限顯得尤為嚴(yán)峻。具體來說,如今的市場發(fā)展趨勢包括:制造的零件的精度更高、零件的形狀和切口有時(shí)非常復(fù)雜、使用超?。ㄐ∮?1 毫米)基板,以及化學(xué)強(qiáng)化玻璃開始出現(xiàn)(機(jī)械法尚不支持切割這種玻璃)。
激光切割的優(yōu)點(diǎn)
目前,用于玻璃切割的激光技術(shù)有許多種,并且這些技術(shù)的實(shí)現(xiàn)方式多種多樣。不過,所有這些玻璃激光切割技術(shù)的主要優(yōu)點(diǎn)都有一些類似。
首先,所有激光切割法都采用非接觸式加工工藝,這就大大避免了細(xì)微裂紋和碎屑的問題。另外,激光切割法留在玻璃中的殘余應(yīng)力極?。ú煌懈罘ǖ臍堄鄳?yīng)力有所不同),因而切割邊緣的強(qiáng)度更高。這一點(diǎn)非常重要,如果殘余應(yīng)力太大,那么即使在玻璃板中心施力,往往也會(huì)導(dǎo)致玻璃邊緣發(fā)生破裂。因此,與采用機(jī)械法切割的玻璃相比,激光切割的玻璃能承受的力要大一到兩倍。
圖 1. 機(jī)械切割玻璃(左圖)與激光切割玻璃(右圖)比較。圖中顯示,機(jī)械切割玻璃存在相當(dāng)大的殘余應(yīng)力,并且切割過程留下了大量碎屑。
由于很少需要(或完全不需要)后續(xù)清潔或打磨階段的工作,因此激光切割還可以減少工藝環(huán)節(jié)的數(shù)量。因此,雖然激光切割工作臺(tái)的資本成本比機(jī)械系統(tǒng)高,但由于不需要額外配備打磨機(jī),所以激光切割的總投資要比機(jī)械加工系統(tǒng)低。由于對后處理工作和清潔工作的需求下降,因此激光切割法比機(jī)械法更環(huán)保,耗用的水資源也更少(或完全不需要耗用水資源)。
最后,有些激光切割法支持玻璃曲線切割。如今對曲線切割的需求量越來越大,尤其在手機(jī)制造行業(yè),制造商們希望生產(chǎn)幾何形狀更復(fù)雜的屏幕,包括在材料上打孔來容納按鍵、控制鍵、LED 和相機(jī)鏡頭。
CO2 和 CO 激光器
二氧化碳 (CO2) 激光器用于切割玻璃已有多年。相比之下,作為工業(yè)實(shí)用型工具的一氧化碳 (CO) 激光器直到 2015 年才由相干公司率先推出,可算是剛剛開始在這一應(yīng)用領(lǐng)域的部署。不論是 CO2 激光器還是 CO 激光器,都有玻璃切割速度快、產(chǎn)量大的優(yōu)點(diǎn)。
CO2 和 CO 激光源加工玻璃的原理都是在局部密集加熱。具體來說,所有玻璃都極易吸收 CO2 激光器產(chǎn)生的 10.6 微米波長,因此聚焦的激光束能夠快速加熱玻璃表面或近表面區(qū)域。為了實(shí)現(xiàn)切割效果,玻璃需要相對激光束平移,并且由玻璃上方的噴液或噴氣口對玻璃進(jìn)行快速冷卻。由此帶來的熱沖擊會(huì)讓玻璃形成連續(xù)切縫。如果玻璃較薄,切縫可以完全穿透基板,從而直接完成切割,這叫做“整體切割”。如果玻璃比較厚,那么還需要額外通過一個(gè)激光或機(jī)械式掰斷環(huán)節(jié)才能完成切割,這叫做“激光劃線”。
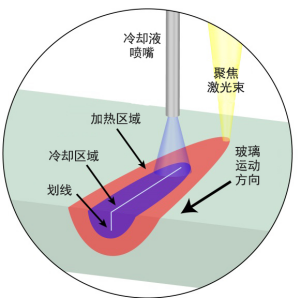
圖 2. CO2 激光器劃線示意圖。
CO 激光器的總體加工過程大致同上。不過,玻璃對 CO 激光器輸出的 5 微米到 6 微米激光的吸收率顯著降低,這讓激光照射大塊材料時(shí)能夠穿透得更深。因此,熱量能夠直接深入大塊玻璃,而無需依靠從表面?zhèn)鞑?。相干公司開展的測試表明,這能比使用 CO2 激光器進(jìn)一步降低殘余應(yīng)力,從而提高切割工件的強(qiáng)度,同時(shí)讓制造商能夠擴(kuò)大加工區(qū)間。
CO 激光器還有一個(gè)吸引人的優(yōu)點(diǎn)是支持曲線切割。CO2 激光器往往局限于以直線切割玻璃,因?yàn)槠鋱A形輸出光束必須重塑為細(xì)長光線,才能更好地發(fā)散表面產(chǎn)生的高溫。相比之下,CO 激光器吸收率較低的特點(diǎn)讓它能直接使用圓形光束,而且不會(huì)產(chǎn)生不利的熱影響。另外,CO 激光器還支持切割化學(xué)強(qiáng)化玻璃。
圖 3. 輸出功率僅 9 瓦的 CO 激光器以 140 毫米/秒的加工速率,在超薄玻璃(厚度 50 微米)上實(shí)現(xiàn)平滑整齊的曲線切割效果(半徑 6 毫米的圓)。
激光燒蝕
激光燒蝕的玻璃加工機(jī)制與通過熱沖擊形成切縫的 CO2 和 CO 激光器完全不同。激光燒蝕實(shí)現(xiàn)劃線的方式是通過精準(zhǔn)燒蝕真正去除材料。當(dāng)施加功率足夠大的激光,從而在玻璃中激發(fā)非線性吸收時(shí),就會(huì)實(shí)現(xiàn)燒蝕。這樣一來,就能通過局部密集加熱(熱燒蝕)或通過極高峰值功率直接破壞原子間化學(xué)鍵(光燒蝕)來去除材料。
用于激光燒蝕的激光器要么是脈寬在納秒級的 Q 開關(guān)半導(dǎo)體泵浦固體激光器,要么是脈寬在皮秒乃至飛秒級的工業(yè)超快激光器。這些工業(yè)超快激光器往往使用鎖模半導(dǎo)體泵浦固體激光器作為種子來實(shí)現(xiàn)后續(xù)的一級或多級放大。
通過激光燒蝕來切割玻璃存在許多不同形式,不過所有這些形式有個(gè)共同點(diǎn),那就是激光脈沖會(huì)從基板上打下微小碎屑。通常,脈寬與去除的顆粒的大小有直接關(guān)聯(lián)。脈寬為納秒級的激光器產(chǎn)生的碎屑大小以數(shù)微米為單位,超快激光器產(chǎn)生的顆粒以數(shù)百納米為單位。
納秒脈寬激光器發(fā)射的綠光(532 納米)或紫外光(355 納米)往往會(huì)穿透透明基板頂層,并且最初聚焦于底部表面。在這種所謂的“自下而上”方法中,燒蝕下來的碎屑會(huì)受重力作用從材料相互作用區(qū)域掉落。通過沿預(yù)期輪廓移動(dòng)貫穿基板的聚焦光束,刻劃或切割邊緣幾乎可以是任何邊緣輪廓,包括曲線切割、槽、孔、溝槽、斜面和切面。
與其他方法相比,這類燒蝕方法的加工速度比較慢。舉例來說,用這種方法在厚度 3 毫米的鈉鈣玻璃上鉆一個(gè)直徑 1 毫米的孔大約需要 1 秒鐘。切割自由輪廓的速度為每秒鐘幾毫米。這種方法的缺陷還包括無法加工強(qiáng)化玻璃,而且加工邊緣往往存在大小約在 10 微米到 50 微米的較大碎屑。
圖 4. 采用“自下而上”方法加工的通孔
超快激光器的劃線過程通常是激光首先聚焦于基板上表面,然后通過調(diào)整光束聚焦點(diǎn)讓加工深度達(dá)到穿透整個(gè)材料。由于切割過程中產(chǎn)生的微小顆粒不能自動(dòng)從劃片掉落(雖然通過一定方法可以去除這些顆粒),因此超快激光器難以實(shí)現(xiàn)“自下而上”的鉆孔或切割。除了切割速度較慢和邊緣較粗糙這兩個(gè)局限性之外,使用超快激光器進(jìn)行頂部劃線的局限性還包括劃片和孔始終會(huì)存在范圍通常在 8° 到 12° 的錐度。
在超快激光器中,飛秒激光器的切割質(zhì)量已被證明優(yōu)于皮秒激光器,不過由于工業(yè)激光器提供的平均功率較低,飛秒激光器的切割速度往往更慢。
SmartCleave 成絲切割
玻璃切割也能通過特定形式的內(nèi)部變形來實(shí)現(xiàn)。這個(gè)過程叫做“成絲”,同樣需要利用由超快激光器聚焦光束提供的超高功率密度。在這個(gè)過程中,受非線性克爾光學(xué)效應(yīng)影響,超高密度的激光光束會(huì)產(chǎn)生自聚焦現(xiàn)象。這種自聚焦會(huì)進(jìn)一步提高功率密度,直到達(dá)到某一閾值后在材料中產(chǎn)生低密度等離子體。這種等離子體會(huì)降低材料在光束路徑中間的折射率,并會(huì)造成光束散焦。通過適當(dāng)配置光束聚焦光學(xué)部件,可以讓這種聚焦/散焦效應(yīng)達(dá)到平衡,從而實(shí)現(xiàn)周期性重復(fù)并在光學(xué)透明材料中形成長達(dá)數(shù)毫米、較為穩(wěn)定的光絲。這種光絲的直徑通常在 0.5 微米到 1 微米之間。

圖 5. 激光光絲在厚度為 0.5 毫米的藍(lán)寶石中形成一系列平行空隙。
為了有效得到零間隙切割或穿孔線,需要移動(dòng)工件與激光光束之間的相對位置,讓激光生成的光絲彼此靠近。根據(jù)材料厚度和需要的切割幾何圖形,切割速度可以達(dá)到 100 毫米/秒至 2000 毫米/秒。
Coherent | Rofin 利用成絲技術(shù)研發(fā)的代表性技術(shù)叫作 SmartCleave。這一技術(shù)由 Rofin 在采購的工藝技術(shù)基礎(chǔ)上進(jìn)一步研發(fā),然后搭配相干公司的高級工業(yè)超快激光器形成。最終形成的工藝可快速切割任意形狀、厚度為 0.05 毫米到 10 毫米的透明脆性材料(包括曲線切割、自由形式切割和內(nèi)嵌切割),并且無錐度產(chǎn)生。SmartCleave 的切割面平滑,Ra 小于 1 微米,并且無缺口和碎屑。與機(jī)械式工藝相比,這樣得到的切割工件的彎曲強(qiáng)度更高。
對于非強(qiáng)化透明玻璃(例如鈉鈣玻璃、硼硅酸鹽玻璃和鋁硅酸鹽玻璃)以及藍(lán)寶石,在成絲之后還需增加一個(gè)分離環(huán)節(jié)。這可以通過施加一個(gè)不大的機(jī)械力或溫差力來實(shí)現(xiàn)。例如,后者可以由 CO2 激光器加熱來提供。對于化學(xué)強(qiáng)化或熱強(qiáng)化玻璃,工件內(nèi)部的應(yīng)力可以實(shí)現(xiàn)自動(dòng)沿外部輪廓分離,因此無需再額外增加其他環(huán)節(jié)。
圖 6. SmartCleave 支持快速對玻璃進(jìn)行曲線切割和內(nèi)嵌切割,例如切割用于顯示屏基板的玻璃。
實(shí)施 SmartCleave
隨著相干公司于 2016 年收購 Rofin,SmartCleave 技術(shù)現(xiàn)已融入相干公司的工業(yè)超快激光器系列,包括 HYPERRAPID 系列。這些產(chǎn)品提供了輸出功率、可靠性和操作靈活性的獨(dú)特組合,包括支持突發(fā)模式和按需脈沖操作。因此,在特定應(yīng)用環(huán)境中有效實(shí)施成絲切割的能力達(dá)到了無以倫比的水平。
另外,Coherent | Rofin 提供各種產(chǎn)品以多種多樣的集成配置支持 SmartCleave 加工。首先是激光源,例如 HYPERRAPID 系列產(chǎn)品。我們還提供將激光器與光束傳輸光學(xué)部件和控制電子器件集成在一起的子系統(tǒng)。另外,可以將這些器件配置為所謂的“黑盒”子系統(tǒng),也就是針對特定工藝提供現(xiàn)成的特定配置。這些配置已開發(fā)和編程完畢,能夠支持和優(yōu)化這一特定工藝。最后,Coherent | Rofin 還能提供完善、即時(shí)可用的系統(tǒng)來實(shí)現(xiàn) SmartCleave 工藝,并且這些系統(tǒng)隨時(shí)能夠在生產(chǎn)環(huán)境中投入使用。
總之,實(shí)踐證明,激光器是能在廣泛應(yīng)用環(huán)境中代替?zhèn)鹘y(tǒng)玻璃切割技術(shù)的可行替代方案。一般來說,在機(jī)械法不能提供所需的切割質(zhì)量或特征,或者舊方法因需要大量后期處理而變得過于昂貴時(shí),激光器的優(yōu)勢最大。然而,玻璃激光切割涉及的范圍很廣,涵蓋多種不同的技術(shù),并且每種技術(shù)都有其獨(dú)特的特征和優(yōu)點(diǎn)。作為唯一一家?guī)缀跄芴峁┧胁A懈罴す馄鞯墓?yīng)商,相干公司占據(jù)獨(dú)一無二的優(yōu)勢地位,能夠?yàn)榫唧w應(yīng)用環(huán)境提供最佳解決方案。對于 SmartCleave 成絲切割,相干公司將受專利保護(hù)的技術(shù)知識(shí)與卓越的激光技術(shù)相結(jié)合,滿足在生產(chǎn)環(huán)境中成功實(shí)現(xiàn)這一卓越技術(shù)的相關(guān)要求。
作者信息
Roland Mayerhofer,Coherent | ROFIN
R.Mayerhofer@rofin.de
George Oulundsen,相干公司
George.oulundsen@coherent.com
Rainer Paetzel,相干公司
rainer.paetzel@coherent.com
轉(zhuǎn)載請注明出處。