摩托車是一種應(yīng)用廣、快速、經(jīng)濟(jì)、舒適的交通和運(yùn)動(dòng)工具,它具有靈活、輕便、機(jī)動(dòng)和高速等特點(diǎn)。隨著科學(xué)技術(shù)的發(fā)展,現(xiàn)代摩托車產(chǎn)業(yè)已經(jīng)融合了機(jī)電液技術(shù)、信息與數(shù)字化技術(shù)、控制與測試技術(shù)、新工藝技術(shù)和新材料技術(shù)等諸多高新技術(shù),成為了一種技術(shù)含量很高的產(chǎn)品。
在摩托車生產(chǎn)制造各環(huán)節(jié)中,激光加工技術(shù)大有用武之處。涉及摩托車制造的激光加工技術(shù)主要有激光表面改性處理(包括激光相變硬化、熔覆、合金化)、激光打孔、激光切割、激光焊接、激光沖擊以及激光打標(biāo)、激光刻花、激光測量等。
激光相變硬化處理(激光淬火)
激光相變硬化處理(Laser Transformation Hardening, LTH)是激光表面改性處理中最早使用的方法,由于激光加熱能把熱量限制在所需要的部位,所以激光相變硬化時(shí)變形極小(約為15~20),可獲得極薄的均勻硬化層(一般小于1mm)。由于金屬材料對激光吸收率低(對CO2激光吸收率低于10%,對YAG激光吸收率最高為30~40%),因而激光相變硬化時(shí),為提高材料表面對激光吸收率,可在表面涂上一層涂料,使金屬表面對激光吸收率達(dá)90%以上。激光適用于對變形很敏感的零件的特殊部位(如深孔內(nèi)壁、盲孔底部等)進(jìn)行硬化處理。
摩托車發(fā)動(dòng)機(jī)排量大多在50~750cm3,其絕大部分關(guān)鍵件結(jié)構(gòu)與要求均與汽車發(fā)動(dòng)機(jī)相似。目前在歐美、日本等發(fā)達(dá)國家已將激光技術(shù)用于汽車、航空等工業(yè)領(lǐng)域,相比之下,我國在這方面存在較大的差距,尤其是在摩托車行業(yè)中。
早在1978年美通用汽車公司建成了汽缸激光處理生產(chǎn)線,用4臺5kw的CO2激光器對鑄鐵缸套內(nèi)壁處理出寬為2.5mm,深為0.5mm的螺旋線硬化帶,并規(guī)定缸套必須經(jīng)激光處理才能出廠。
北京大恒公司對汽車發(fā)動(dòng)機(jī)缸體內(nèi)壁進(jìn)行激光硬化處理,采用激光功率為900w,掃描速度為400mm/S,激光硬化帶寬3.5mm,深0.25~0.3mm,硬度達(dá)HRC63,將使用壽命提高了3倍。青島發(fā)動(dòng)機(jī)廠對6102Q高速柴油機(jī)缸體進(jìn)行激光相變硬化處理,省去了缸套,缸孔內(nèi)表面耐磨性超過硼缸套16%~20%。
1984年前蘇聯(lián)卡基諾論汽車修理廠采用激光對3號鋼和45號鋼的曲軸進(jìn)行激光相變處理。經(jīng)90小時(shí)臺架試驗(yàn),主軸頸和連桿軸頸的平均磨損量較傳統(tǒng)熱處理方法分別減少47.3%和43.5%,一般運(yùn)行時(shí)耐磨性增加42%、疲勞強(qiáng)度提高15%、主軸頸壽命延長10%。1985年,長春第一汽車廠使用1.8kw激光器對45號鋼的曲軸軸頸進(jìn)行掃描相變硬化處理,獲得寬為3.8mm,深為0.8~1.37mm的淬火帶,硬度達(dá)765HV。1994年大連機(jī)車車輛廠對曲軸的主軸頸和連桿軸頸部分進(jìn)行激光處理,使相變硬化中心帶表面殘余應(yīng)力達(dá)—(900~1000)Mpa,再配合表面滾壓,使疲勞壽命提高185%以上。
華南理工大學(xué)對汽車發(fā)動(dòng)機(jī)排氣閥進(jìn)行激光硬化處理,獲得了滿意的效果以取代價(jià)格昂貴的進(jìn)口零件,完成標(biāo)致汽車的國產(chǎn)化,1997年華南師大量子電子研究所對材料為的排氣閥尾端進(jìn)行相變硬化處理,其硬化層厚度和硬度值均達(dá)到了標(biāo)致汽車機(jī)排氣閥圖紙規(guī)定的要求。
目前凸輪軸激光表面處理主要用于小型發(fā)動(dòng)機(jī)上,對凸輪表面的一定節(jié)距進(jìn)行激光螺旋掃描處理,獲得硬化骨架和軟化貯油溝槽兼?zhèn)涞谋砻?,以提高耐磨和耐擦傷性能。?992年德國開始在凸輪軸上旋行激光重熔淬火處理,得到萊氏體組織,凸輪耐磨性和接觸疲勞強(qiáng)度均得到了顯著的提高。
日本日產(chǎn)公司(特開昭963—134634專利)提出用條狀激光束沿凸輪寬度進(jìn)行激光掃描相變處理,這樣可獲得均勻組織,又不會(huì)出現(xiàn)兩側(cè)塌邊現(xiàn)象。處理后表面組織為枝晶狀細(xì)萊氏體,表面硬度高過800~1000HV以上,達(dá)到550HV有效硬化層厚度超過1.5mm。試驗(yàn)表明這種組織具有很高的接觸疲勞強(qiáng)度和耐磨損、耐腐蝕、耐擦傷性能,是一種理想的凸輪軸強(qiáng)化方法。
1997年天津大學(xué)對灰鑄鐵凸輪軸進(jìn)行了激光重熔強(qiáng)化處理。試驗(yàn)是在6kw連續(xù)波CO2激光器上進(jìn)行。結(jié)果表明凸輪經(jīng)激光表面重熔處理后,表層為強(qiáng)化細(xì)萊氏體組織,其硬度顯著高于基體,耐磨性能優(yōu)于冷激鑄鐵。
1999年廣東五邑大學(xué)、江蘇理工大學(xué)和大長江摩托車公司合作,使用NEL2500快速軸流CO2激光器,對HJ125T型摩托車發(fā)動(dòng)機(jī)中與C型環(huán)配合、材料為HT300的凸輪軸頸部,寬6mm、長16mm、深為16mm的槽底進(jìn)行激光相變處理,處理后的零件經(jīng)硬度測量、耐磨損和耐沖擊試驗(yàn)以及金相組織分析表明,其各項(xiàng)性能均達(dá)到日本進(jìn)口零件要求,完全可實(shí)現(xiàn)該零件的國產(chǎn)化。
同時(shí)五邑大學(xué)、江蘇理工大學(xué)還對摩托車發(fā)動(dòng)機(jī)凸輪、正時(shí)鏈輪齒部(材料為20CrMo)進(jìn)行了激光相變硬化處理,不但可以保證質(zhì)量,而且減化工藝流程,降低成本,取得了滿意的效果。
活塞環(huán)是發(fā)動(dòng)機(jī)關(guān)鍵零件之一,采用激光相變處理后可使其表面硬度達(dá)1000HV以上?;钊h(huán)的激光相變處理與鍍鉻、鍍鉬、滲碳處理相比,具有工藝簡單、生產(chǎn)效率高、無三廢污染和節(jié)約貴金屬等優(yōu)點(diǎn),實(shí)際應(yīng)用中取得了良好的效果。如我國戚墅堰機(jī)車車輛工藝所與原長沙鐵道學(xué)院對鉻鉬銅合金鑄鐵活塞環(huán)進(jìn)行相變硬化處理,表面硬度達(dá)800~1260HV,裝車后進(jìn)行18~21萬余公里檢測表明,最嚴(yán)重的第一氣環(huán)磨損量僅為0.005~0.0125mm/104km,且潤滑油消耗量降低了23%~25%,取得了可觀的經(jīng)濟(jì)效益。日本洋馬公司用1kw級的CO2激光器對M200型發(fā)動(dòng)機(jī)用的球墨鑄鐵活塞環(huán)進(jìn)行了激光淬火處理,取得了良好的效果。
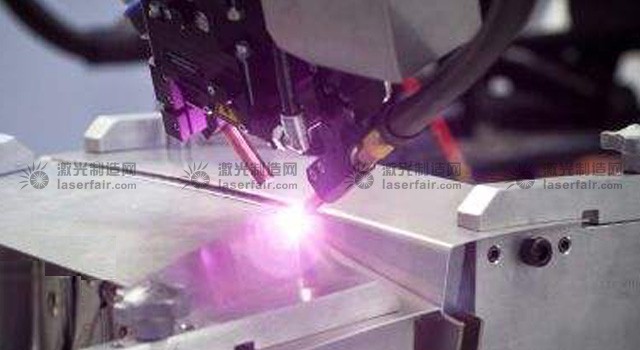
待續(xù)…
連載技術(shù)文章,有興趣的讀者近期敬請關(guān)注本公眾號推文!
轉(zhuǎn)載請注明出處。